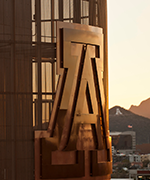
Erica L Corral
- Professor, Materials Science and Engineering
- Professor, BIO5 Institute
- Distinguished Scholar, Materials Science and Engineering
- Professor, Aerospace-Mechanical Engineering
- Member of the Graduate Faculty
Contact
- (520) 621-0934
- John W. Harshbarger Building, Rm. 338C
- Tucson, AZ 85721
- elcorral@arizona.edu
Biography
Degrees
- Ph.D. Materials Science
- William Marsh Rice University, Houston, Texas, United States
- Single-walled carbon nanotube reinforced ceramic composites
- B.S. Metallurgical and Materials Engineering
- The University of Texas at El Paso, El Paso, Texas, United States
Work Experience
- Co-Director, University Consortium for Applied Hypersonics (UCAH)
- Co-Director, Arizona Research Center for Hypersonics (ARCH)
- Distinguished Scholar, The University of Arizona, Tucson, Arizona (2016 - Ongoing)
- Associate Professor, The University of Arizona, Tucson, Arizona (2013 - Ongoing)
- Assistant Professor, The University of Arizona, Tucson, Arizona (2008 - 2013)
- Postdoctoral Research Associate, Sandia National Laboratories (2005 - 2008)
Awards
- NSF CAREER Award, 2010
- AFOSR YIP Award, 2010
- AFOSR MURI Award, Co-PI, 2010
- Dr. Eugene Garcia, Outstanding Latino/a Faculty: Research in High Education Victoria Foundation, 2016
- Distinguished Scholar Award, 2016
- Governance Board, University Consirtum for Applied Hypersonics (UCAH) 2021 & 2022
Degrees
- Ph.D. Materials Science
- William Marsh Rice University, Houston, Texas, United States
- Single-walled carbon nanotube reinforced ceramic composites
- B.S. Metallurgical and Materials Engineering
- The University of Texas at El Paso, El Paso, Texas, United States
Work Experience
- The University of Arizona, Tucson, Arizona (2016 - Ongoing)
- The University of Arizona, Tucson, Arizona (2013 - Ongoing)
- The University of Arizona, Tucson, Arizona (2008 - 2013)
- Sandia National Laboratories (2005 - 2008)
Awards
- Most Influential Paper Award
- Journal of the American Ceramic Society, Fall 2019
- Dr. Eugene Garcia, Outstanding Latino/a Faculty: Research in High Education
- Victoria Foundation, Fall 2016
- Distinguished Scholar
- Spring 2016
Interests
No activities entered.
Courses
2025-26 Courses
-
Mech Behavior of Mat
MSE 370 (Fall 2025)
2024-25 Courses
-
Phys+Chem Ceramic Mat
MSE 424 (Spring 2025) -
Phys+Chem Ceramic Mat
MSE 524 (Spring 2025) -
Mech Behavior of Mat
MSE 370 (Fall 2024)
2023-24 Courses
-
Intro To Mat Sci Engr II
MSE 223R (Spring 2024) -
Mech Behavior of Mat
MSE 370 (Fall 2023)
2022-23 Courses
-
Research
MSE 900 (Spring 2023) -
Thesis
MSE 910 (Spring 2023) -
Mech Behavior of Mat
MSE 370 (Fall 2022) -
Research
MSE 900 (Fall 2022)
2021-22 Courses
-
Independent Study
MSE 399 (Spring 2022) -
Thesis
MSE 910 (Spring 2022) -
Mech Behavior of Mat
MSE 370 (Fall 2021) -
Research
MSE 900 (Fall 2021) -
Senior Capstone
MSE 498 (Fall 2021)
2020-21 Courses
-
Research
MSE 900 (Summer I 2021) -
Fund Materials for Engr
MSE 331R (Fall 2020) -
Mech Behavior of Mat
MSE 370 (Fall 2020)
2019-20 Courses
-
Fund Materials for Engr
MSE 331R (Fall 2019) -
Mech Behavior of Mat
MSE 370 (Fall 2019)
2018-19 Courses
-
Fund Materials for Engr
MSE 331R (Fall 2018) -
Mech Behavior of Mat
MSE 370 (Fall 2018)
2017-18 Courses
-
Dissertation
MSE 920 (Fall 2017) -
Fund Materials for Engr
MSE 331R (Fall 2017) -
Independent Study
MSE 399 (Fall 2017) -
Materials
MSE 595A (Fall 2017)
2016-17 Courses
-
Dissertation
MSE 920 (Spring 2017) -
Fund Materials for Engr
MSE 331R (Spring 2017) -
Honors Thesis
MSE 498H (Spring 2017) -
Materials
MSE 595A (Spring 2017) -
Dissertation
MSE 920 (Fall 2016) -
Fund Materials for Engr
MSE 331R (Fall 2016) -
Materials
MSE 595A (Fall 2016)
2015-16 Courses
-
Dissertation
MSE 920 (Spring 2016) -
Intro To Mat Sci Engr II
MSE 223R (Spring 2016) -
Research
MSE 900 (Spring 2016) -
Senior Capstone
MSE 498 (Spring 2016) -
Spec Tops Mat Sci+Eng
MSE 596A (Spring 2016) -
Thesis
MSE 910 (Spring 2016)
Scholarly Contributions
Journals/Publications
- Corral, E. L., & Miller-Oana, M. (2016). High Temperature Isothermal Oxidation of Ultra-High Temperature Ceramics Using Thermal Gravimetric Analysis. The Journal of the American Ceramic Society, 99, 619-626.
- Corral, E. L., Dycus, H., LeBeau, J., Venkateswara, M., Mulidharan, K., & Pham, D. (2016). Processing Low Oxide Impurity ZrB2 Ceramics with High Strength Using Boron Carbide and Spark Plasma Sintering. The Journal of the American Ceramic Society, 9(8), 2585-2592.
- Corral, E. L., Dycus, J. H., LeBeau, J., Mulidharan, K., Vankateswara, M., & Pham, D. (2016). Processing Low Oxide Impurity ZrB2 Ceramics with High Strength Using Boron Carbide and Spark Plasma Sintering. The Journal of the American Ceramic Society, In press.
- Miller-Oana, M., & Corral, E. L. (2016). High-Temperature Isothermal Oxidation of Ultra-High Temperature Ceramics Using Thermal Gravimetric Analysis. JOURNAL OF THE AMERICAN CERAMIC SOCIETY, 99(2), 619-626.
- Pham, D., Dycus, J. H., LeBeau, J. M., Mulidharan, K., Venkateswara, M., & Corral, E. L. (2016). Processing Low Oxide Impurity ZrB2 Ceramics with High Strength Using Boron Carbide and Spark Plasma Sintering. Journal of the American Ceramic Society, 99(8), 2585-2592.
- Corral, E. L., Miller-Oana, M., Neff, P. K., Valdez, M., Powell, A., & Walker, L. S. (2015). Oxidation Behavior of Aerospace Materials in High Enthalpy Flows Using an Oxyacetylene Torch Facility. The Journal of the American Ceramic Society, 98(4), 1300-1307.
- Miller-Oana, M., Neff, P. K., Valdez, M., Powell, A., Walker, L. S., & Corral, E. L. (2014). Oxidation Behavior of Aerospace Materials in High Enthalpy Flows Using an Oxyacetylene Torch Facility. THE JOURNAL OF THE AMERICAN CERAMIC SOCIETY, Published Online-Early Preview, 1-12.
- Walker, L. S., & Corral, E. L. (2014). Self-Generating High-Temperature Oxidation-Resistant Glass-Ceramic Coatings for C-C Composites Using UHTCs. JOURNAL OF THE AMERICAN CERAMIC SOCIETY, 97(2), 3004-3011.More infoCarbon-carbon (C-C) composites are ideal for use as aerospace vehicle structural materials; however, they lack high-temperature oxidation resistance requiring environmental barrier coatings for application. Ultra high-temperature ceramics (UHTCs) form oxides that inhibit oxygen diffusion at high temperature are candidate thermal protection system materials at temperatures >1600 degrees C. Oxidation protection for C-C composites can be achieved by duplicating the self-generating oxide chemistry of bulk UHTCs formed by a composite effect upon oxidation of ZrB2-SiC composite fillers. Dynamic Nonequilibrium Thermogravimetric Analysis (DNE-TGA) is used to evaluate oxidation in situ mass changes, isothermally at 1600 degrees C. Pure SiC-based fillers are ineffective at protecting C-C from oxidation, whereas ZrB2-SiC filled C-C composites retain up to 90% initial mass. B2O3 in SiO2 scale reduces initial viscosity of self-generating coating, allowing oxide layer to spread across C-C surface, forming a protective oxide layer. Formation of a ZrO2-SiO2 glass-ceramic coating on C-C composite is believed to be responsible for enhanced oxidation protection. The glass-ceramic coating compares to bulk monolithic ZrB2-SiC ceramic oxide scale formed during DNE-TGA where a comparable glass-ceramic chemistry and surface layer forms, limiting oxygen diffusion.
- Walker, L. S., & Corral, E. L. (2014). Structural Influence on the Thermal Conversion of Self-Catalyzed HfB2/ZrB2 Sol-Gel Precursors by Rapid Ultrasonication of Oxychloride Hydrates. JOURNAL OF THE AMERICAN CERAMIC SOCIETY, 97(2), 399-406.More infoSol-gel precursors to HfB2 and ZrB2 are processed by high-energy ultrasonication of Hf,Zr oxychloride hydrates, triethyl borate, and phenolic resin to form precipitate-free sols that turn into stable gels with no catalyst addition. Both precursor concentration and structure (a sol or a gel) are found to influence the synthesis of the diboride phase at high temperature. Decreasing sol concentration increases powder surface area from 3.6 to 6.8m(2)/g, whereas heat-treating a gel leads to residual oxides and carbides. Particles are either fine spherical particles, unique elongated rods, and/or platelets, indicating particle growth with directional coarsening. Investigation of the conversion process to ZrB2 indicates that a multistep reaction is likely taking place with: (1) ZrC formation, (2) ZrC reacts with B2O3 or ZrC reacts with B2O3 and C to form ZrB2. At low temperatures, ZrC formation is limiting, while at higher temperatures the reaction of ZrC to ZrB2 becomes rate limiting. ZrC is found to be a direct reducing agent for B2O3 at low temperature (similar to 1200 degrees C) to form ZrB2 and ZrO2, whereas at high temperatures (similar to 1500 degrees C) it reacts with B2O3 and C to form pure ZrB2.
- Clark, M. D., Walker, L. S., Hadjiev, V. G., Khabashesku, V., Corral, E. L., & Krishnamoorti, R. (2012). Fast Sol-Gel Preparation of Silicon Carbide-Silicon Oxycarbide Nanocomposites. JOURNAL OF THE AMERICAN CERAMIC SOCIETY, 94(12), 4444-4452.More infoSilicon carbide nanofiber dispersion within a silicon oxycarbide glassy ceramic was achieved through a combination of a fast solgel procedure for in situ ceramic matrix synthesis and nanofiber conversion from sacrificial multiwalled carbon nanotube templates. Nanotubes were dispersed using both surfactant adsorption and a covalent sidewall modification scheme with gel-grafting capabilities. The combination of high temperature processing and silicon monoxide precursor concentrations allowed substantial carbothermal reduction of the nanotube templates, yielding silicon carbide nanofibers. The resulting nanocomposites were examined for density, Vickers microhardness, Young's modulus, and fracture toughness. The surfactant-assisted route inhibited ceramic densification, offering virtually no mechanical property enhancement. In contrast, the covalently functionalized nanotube templates at 0.8 wt% loading enhanced tensile modulus of 77% while simultaneously maintaining both Vickers microhardness and fracture toughness. These results indicate strong interfacial adhesion between the nanofiber surface and host matrix despite the abrupt chemical changes experienced during the high temperature processing.
- Clark, M. D., Walker, L. S., Hadjiev, V. G., Khabashesku, V., Corral, E. L., & Krishnamoorti, R. (2012). Polymer Precursor-Based Preparation of Carbon Nanotube-Silicon Carbide Nanocomposites. JOURNAL OF THE AMERICAN CERAMIC SOCIETY, 95(1), 328-337.More infoMultiwalled carbon nanotubes were dispersed in a silicon carbide matrix to examine nanotube influence on mechanical properties of the resulting composite. The ceramic matrix was generated through high temperature conversion of poly(methylsilyne), a preceramic polymeric precursor. Nanotube alkylation was explored using two functionalization schemes: organic peroxide workup and alkyllithium displacement of fluorinated nanotubes, which promoted extensive mixing within precursor solutions, thereby ensuring nanotube dispersion within the polymer matrix while facilitating interfacial bonding. The former scheme was less effective at displacing inner nanotube shell bound fluorine and resulted in lower alkyl chain grafting density on the outer shell. Polymer nanocomposites were pyrolyzed and consolidated using an optimized spark plasma sintering scheme to generate fully densified ceramics. The pure polymer-derived ceramic displayed exceptional Young's modulus and Vickers microhardness of 126 +/- 12 and 9.6 +/- 0.5 GPa, respectively, while maintaining a fracture toughness of 2.8 +/- 0.3 MPa center dot m1/2. Increased sintering time further augmented the fracture toughness to 3.6 +/- 0.4MPa center dot m1/2, approaching the 4MPa center dot m1/2 that characterizes pure silicon carbide, while maintaining both Young's modulus and microhardness. Nanotube addition resulted in some loss of the intrinsic mechanical properties, but enhanced monolith damage tolerance behavior, raising the Vickers indent force needed to induce cracks to an excess of 98.1N in contrast to the pure polymer-derived sample, which began crack propagation below 49.0 N.
- Clark, M. D., Walker, L. S., Hadjiev, V. G., Khabashesku, V., Corral, E. L., & Krishnamoorti, R. (2012). Polymer precursor-based preparation of carbon nanotube-silicon carbide nanocomposites. Journal of the American Ceramic Society, 95(1), 328-337.More infoAbstract: Multiwalled carbon nanotubes were dispersed in a silicon carbide matrix to examine nanotube influence on mechanical properties of the resulting composite. The ceramic matrix was generated through high temperature conversion of poly(methylsilyne), a preceramic polymeric precursor. Nanotube alkylation was explored using two functionalization schemes: organic peroxide workup and alkyllithium displacement of fluorinated nanotubes, which promoted extensive mixing within precursor solutions, thereby ensuring nanotube dispersion within the polymer matrix while facilitating interfacial bonding. The former scheme was less effective at displacing inner nanotube shell bound fluorine and resulted in lower alkyl chain grafting density on the outer shell. Polymer nanocomposites were pyrolyzed and consolidated using an optimized spark plasma sintering scheme to generate fully densified ceramics. The pure polymer-derived ceramic displayed exceptional Young's modulus and Vickers microhardness of 126 ± 12 and 9.6 ± 0.5 GPa, respectively, while maintaining a fracture toughness of 2.8 ± 0.3 MPa·m 1/2. Increased sintering time further augmented the fracture toughness to 3.6 ± 0.4 MPa·m 1/2, approaching the 4 MPa·m 1/2 that characterizes pure silicon carbide, while maintaining both Young's modulus and microhardness. Nanotube addition resulted in some loss of the intrinsic mechanical properties, but enhanced monolith damage tolerance behavior, raising the Vickers indent force needed to induce cracks to an excess of 98.1 N in contrast to the pure polymer-derived sample, which began crack propagation below 49.0 N. © 2011 The American Ceramic Society.
- Natividad, S. L., Marotto, V. R., Walker, L. S., Pham, D., Pinc, W., & Corral, E. L. (2012). Tape Casting Thin, Continuous, Homogenous, and Flexible Tapes of ZrB2. JOURNAL OF THE AMERICAN CERAMIC SOCIETY, 94(9), 2749-2753.More infoUsing an organic solvent-based formulation, flexible and homogeneous ZrB2 tapes were cast for potential use as advanced aerospace exploration vehicles. Dispersant concentrations were optimized for attrition-milled ZrB2 powder using gravitational sedimentation and viscosity measurements. Tape cast slurry formulations with varying amounts of binder (6-8 vol%), plasticizer (7-11 vol%), and solids loading (20-23 vol%) were used to optimize the casting slurry. An optimal slurry formulation was determined based on cast tape uniform particle distribution and flexibility without cracking. Thermal gravimetric analysis of the optimized tape was used to create a binder burnout schedule that did not alter the tape structure or particle distribution. Our organic solvent-based tape casting approach results in minimum oxygen contamination after colloidal processing and robust cast tapes with a thickness of 280 mu m and green density of similar to 41% theoretic density after binder burnout.
- Walker, L. S., Miller, J. E., Hilmas, G. E., Evans, L. R., & Corral, E. L. (2012). Coextrusion of zirconia-iron oxide honeycomb substrates for solar-based thermochemical generation of carbon monoxide for renewable fuels. Energy and Fuels, 26(1), 712-721.More infoAbstract: Ceramic honeycombs based on homogeneous composites of zirconia and iron oxide are formed using polymer-based coextrusion for testing in thermochemical reactors to generate CO for renewable fuels. The honeycomb substrates possess controlled surface areas and are processed using zirconia with 3 and 8 mol % yttria additions to investigate the influence of surface area and oxygen conductivity of the substrate on the CO generation properties. CO generation was tested using a gas chromatography mass spectrometer and a laboratory scale thermochemical reactor capable of precisely controlling temperature and gas conditions. Results showed that reaction temperature and reactant gas flow rate effect CO generation. The yttria content of the zirconia support phase was also found to have a significant impact on the long-term CO generation, improving iron oxide conversion from 41 to 58%. Yttria content did not markedly impact the short-term reaction properties. Increasing the surface area of the substrates, from 2.6 up to 8.5 cm 2, did not result in improvements in CO generation within the resolution of the test equipment. The substrates reacted by two distinct mechanisms, an initial, spontaneous surface reaction that changed over time to a diffusion-based mechanism utilizing reaction material from the bulk. These substrate systems exhibit the high reactivity necessary for large-scale thermochemical reactors, while being based on common materials. © 2011 American Chemical Society.
- Clark, M. D., Walker, L. S., Hadjiev, V. G., Khabashesku, V., Corral, E. L., & Krishnamoorti, R. (2011). Fast sol-gel preparation of silicon carbide-silicon oxycarbide nanocomposites. Journal of the American Ceramic Society, 94(12), 4444-4452.More infoAbstract: Silicon carbide nanofiber dispersion within a silicon oxycarbide glassy ceramic was achieved through a combination of a fast sol-gel procedure for in situ ceramic matrix synthesis and nanofiber conversion from sacrificial multiwalled carbon nanotube templates. Nanotubes were dispersed using both surfactant adsorption and a covalent sidewall modification scheme with gel-grafting capabilities. The combination of high temperature processing and silicon monoxide precursor concentrations allowed substantial carbothermal reduction of the nanotube templates, yielding silicon carbide nanofibers. The resulting nanocomposites were examined for density, Vickers microhardness, Young's modulus, and fracture toughness. The surfactant-assisted route inhibited ceramic densification, offering virtually no mechanical property enhancement. In contrast, the covalently functionalized nanotube templates at 0.8 wt% loading enhanced tensile modulus of 77% while simultaneously maintaining both Vickers microhardness and fracture toughness. These results indicate strong interfacial adhesion between the nanofiber surface and host matrix despite the abrupt chemical changes experienced during the high temperature processing. © 2011 The American Ceramic Society.
- Corral, E. L., Wang, H., Garay, J., Munir, Z., & Barrera, E. V. (2011). Effect of single-walled carbon nanotubes on thermal and electrical properties of silicon nitride processed using spark plasma sintering. Journal of the European Ceramic Society, 31(3), 391-400.More infoAbstract: Si3N4 nanocomposites reinforced with 1-, 2-, and 6-vol% single-walled carbon nanotubes (SWNTs) were processed using spark plasma sintering (SPS) in order to control the thermal and electrical properties of the ceramic. Only 2-vol% SWNTs additions were used to decrease the room temperature thermal conductivity by 62% over the monolith and 6-vol% SWNTs was used to transform the insulating ceramic into a metallic electrical conductor (92Sm-1). We found that densification of the nanocomposites was inhibited with increasing SWNT concentration however, the phase transformation from α- to β-Si3N4 was not. After SPS, we found evidence of SWNT survival in addition to sintering induced defects detected by monitoring SWNT peak intensity ratios using Raman spectroscopy. Our results show that SWNTs can be used to effectively increase electrical conductivity and lower thermal conductivity of Si3N4 due to electrical transport enhancement and thermal scattering of phonons by SWNTs using SPS. © 2010 Elsevier Ltd.
- Corral, E., Walker, L. S., Marotto, V. R., Rafiee, M. A., Koratkar, N., & Corral, E. L. (2011). Toughening in graphene ceramic composites. ACS nano, 5(4).More infoThe majority of work in graphene nanocomposites has focused on polymer matrices. Here we report for the first time the use of graphene to enhance the toughness of bulk silicon nitride ceramics. Ceramics are ideally suited for high-temperature applications but suffer from poor toughness. Our approach uses graphene platelets (GPL) that are homogeneously dispersed with silicon nitride particles and densified, at ∼1650 °C, using spark plasma sintering. The sintering parameters are selected to enable the GPL to survive the harsh processing environment, as confirmed by Raman spectroscopy. We find that the ceramic's fracture toughness increases by up to ∼235% (from ∼2.8 to ∼6.6 MPa·m(1/2)) at ∼1.5% GPL volume fraction. Most interestingly, novel toughening mechanisms were observed that show GPL wrapping and anchoring themselves around individual ceramic grains to resist sheet pullout. The resulting cage-like graphene structures that encapsulate the individual grains were observed to deflect propagating cracks in not just two but three dimensions.
- Walker, L. S., Miller, J. E., Hilmas, G. E., Evans, L. R., & Corral, E. L. (2011). Coextrusion of Zirconia-Iron Oxide Honeycomb Substrates for Solar-Based Thermochemical Generation of Carbon Monoxide for Renewable Fuels. ENERGY & FUELS, 26(1), 712-721.More infoCeramic honeycombs based on homogeneous composites of zirconia and iron oxide are formed using polymer-based coextrusion for testing in thermochemical reactors to generate CO for renewable fuels. The honeycomb substrates possess controlled surface areas and are processed using zirconia with 3 and 8 mol % yttria additions to investigate the influence of surface area and oxygen conductivity of the substrate on the CO generation properties. CO generation was tested using a gas chromatography mass spectrometer and a laboratory scale thermochemical reactor capable of precisely controlling temperature and gas conditions. Results showed that reaction temperature and reactant gas flow rate effect CO generation. The yttria content of the zirconia support phase was also found to have a significant impact on the long-term CO generation, improving iron oxide conversion from 41 to 58%. Yttria content did not markedly impact the short-term reaction properties. Increasing the surface area of the substrates, from 2.6 up to 8.5 cm(2), did not result in improvements in CO generation within the resolution of the test equipment. The substrates reacted by two distinct mechanisms, an initial, spontaneous surface reaction that changed over time to a diffusion-based mechanism utilizing reaction material from the bulk. These substrate systems exhibit the high reactivity necessary for large-scale thermochemical reactors, while being based on common materials.
- Walker, L. S., Pinc, W. R., & Corral, E. L. (2012). Powder Processing Effects on the Rapid Low-Temperature Densification of ZrB2-SiC Ultra-High Temperature Ceramic Composites Using Spark Plasma Sintering. JOURNAL OF THE AMERICAN CERAMIC SOCIETY, 95(1), 104-203.More infoInvestigating the powder processing effects on a ZrB(2)25 similar to vol% SiC ceramic composite densified using spark plasma sintering (SPS) allows for identification of densification mechanisms and enables a reduction in sintering temperature to a minimum of 1650 degrees C. Attrition milling (AM) and ball milling (BM) were investigated as processing methods to produce a fine and coarse powder densified using SPS with or without a tube furnace preheat treatment. Ceramics formed from AM and BM powders contain 1.66 similar to wt% oxygen contamination, primarily ZrO2 and SiO2, and 0.35 similar to similar to wt% oxygen contamination as SiO2, respectively. Heat treatment slightly reduces oxygen contamination but has significant impacts on the densification mechanisms. Without heat treatment, powder coarsening dominates the initial sintering process in the SPS inhibiting densification until similar to 1350 degrees C. After heat treatment, sintering and densification is enabled at low temperature, 1000 degrees C1100 degrees C. The densification of ZrB2SiC composites can be broken into a two-step process with phase 1 as the sintering step based on powder surface area reduction and phase 2 as a forging step where high-temperature creep and pressure eliminate porosity after the primary grains have formed. A timetemperature-density plot illustrates the change in densification mechanism used to fully densify ZrB2SiC composites in SPS.
- Corral, E. L. (2010). Multifunctional silicon nitride ceramic nanocomposites using single-walled carbon nanotubes. Ceramic Engineering and Science Proceedings, 30(7), 17-25.More infoAbstract: High-temperature ceramics, such as silicon nitride, are considered the best-suited materials for use in extreme environments because they posess high melting temperatures, high strength and toughness, and good thermal shock resistance. The goal of this research is to create bulk multifunctional high-temperature ceramic nanocomposites using single-wall carbon nanotubes in order to tailor electrical and thermal conductivity properties, while also enhancing the mechanical properties of the monolith. Colloidal processing methods were used to develop aqueous single-walled carbon nanotube (SWNT)-Si3N4 suspensions that were directly fabricated into bulk parts using a rapid prototyping method. High-density sintered nanocomposites were produced using spark plasma sintering, at temperatures greater than 1600 °C, and evidence of SWNTs in the final sintered microstructure was observed using scanning electron microscopy and Raman spectroscopy. The multifunctional nanocomposites show exceptional fracture toughness (8.48 MPa-m1/2) properties and was directly measured using conventional fracture toughness testing methods (ASMT C41 ). Our results suggest that the use of SWNTs in optimized sintered ceramic microstructures can enhance the toughness of the ceramic by at least 30% over the monolith. In addition, the observation of hallmark toughening mechanisms and enhanced damage tolerance behavior over the monolith was directly observed. The nanocomposites also measured for reductions in electrical resistivity values over the monolith, making them high-temperature electrical conductors. These novel nanocomposites systems have enhanced electrical conductivity, and enhanced toughness over the monolith which make them unique high-temperature multifunctional nanocomposites.
- Corral, E. L., & Walker, L. S. (2010). Improved ablation resistance of C-C composites using zirconium diboride and boron carbide. Journal of the European Ceramic Society, 30(11), 2357-2364.More infoAbstract: Zirconium diboride and boron carbide particles were used to improve the ablation resistance of carbon-carbon (C-C) composites at high temperature (1500°C). Our approach combines using a precursor to ZrB2 and processing them with B4C particles as filler material within the C-C composite. An oxyacetylene torch test facility was used to determine ablation rates for carbon black, B4C, and ZrB2-B4C filled C-C composites from 800 to 1500°C. Ablation rates decreased by 30% when C-C composites were filled with a combination of ZrB2-B4C particles over carbon black and B4C filled C-C composites. We also investigated using a sol-gel precursor method as an alternative processing route to incorporate ZrB2 particles within C-C composites. We successfully converted ZrB2 particles within C-C composites at relatively low temperatures (1200°C). Our ablation results suggest that a combination of ZrB2-B4C particles is effective in inhibiting the oxidation of C-C composites at temperatures greater than 1500°C. © 2010 Elsevier Ltd.
- Fuller, J., Hilmas, G., Fahrenholtz, W., Corral, E., & Riegel, L. (2010). Guest Editorial. Journal of the European Ceramic Society, 30(11), 2145-2146.
- Pinc, W. R., Di Prima, M., Walker, L. S., Wing, Z. N., & Corral, E. L. (2010). Spark Plasma Joining of ZrB2-SiC Composites Using Zirconium-Boron Reactive Filler Layers. JOURNAL OF THE AMERICAN CERAMIC SOCIETY, 94(11), 3825-3832.More infoSpark plasma joining is used to join ZrB2-SiC composites with seamless microstructures at the joint that results in retention of high-temperature mechanical and oxidation properties after joining. Our approach uses a spark plasma sintering furnace and Zr-B powder filler layers to join the parts together. The joining processing parameters used to optimize the joint microstructure were filler composition, target temperature, hold time, and volume of filler. A filler of 1 mm(3) and spark plasma joining conditions at 1800 degrees C for 300 s resulted in the formation of a joint region that was indistinguishable from the bulk substrates. Room and high-temperature (1350 degrees C) shear strengths of joined substrates measured equal to baseline substrates and oxidation behavior for joined and baseline substrates were equivalent after static air oxidation at 1700 degrees C. X-Ray diffraction measurements show the joint is composed of ZrB2 and ZrC. We found the joining mechanism to be solid-state bonding of ZrB2 that formed from the Zr-B filler and reaction bonding by the formation of ZrC. Spark plasma joining rapidly joins ZrB2-SiC and probably other conductive ultra high-temperature ceramic composites, and has the potential to impact the rapid assembly and joining of complex thermal protection material systems.
- Widgeon, S. J., Corral, E. L., Spilde, M. N., & Loehman, R. E. (2009). Glass-to-Metal seal interfacial analysis using electron probe microscopy for reliable solid oxide fuel cells. Journal of the American Ceramic Society, 92(4), 781-786.More infoAbstract: The chemical compatibility between sealing glasses and interconnect materials for solid oxide fuel cells (SOFCs) has been studied in SOFC environments. Two borate-based glass compositions were sealed to interconnect materials, 441 stainless-steel (441SS) and Mn 1.5Co 1.5O 4-coated 441SS. The Mn 1.5Co 1.5O 4-coated 441SS coupons were analyzed as-received using X-ray diffraction (XRD) and electron probe microanalysis (EPMA) to obtain structural information and concentration profiles, respectively. The concentration profiles and the lack of Fe-containing phases present in the XRD spectrum show Fe is present throughout the coating, suggesting that Fe is partially substituted in the Mn 1.5Co 1.5O 4 spinel. The glass-metal coupons were heat treated in air at 750°C for 500 h. The specimens were analyzed by EPMA and scanning electron microscope (SEM) to obtain images of the glass microstructure at the interface, to verify seal adherence, and to record concentration profiles across the glass-metal interface, with an emphasis on Cr. In total, four seal configurations were tested and analyzed, and in all cases the glasses remained well adhered to the metal and coating, and there was no microstructural evidence of new reaction phases present at the interface. There was slight diffusion of Cr from the 441SS into the sealing glasses, and Cr diffusion was hindered by the coating on the coated 441SS samples. © 2009 The American Ceramic Society.
- Corral, E. L. (2008). Ultra-high temperature ceramic coatings. Advanced Materials and Processes, 166(10), 30-32.More infoAbstract: Multilayer ceramin coatings appear to offer the best oxidation protection for carbon-carbon composites that make up the structure of future hypersonic spcae vehicles.
- Corral, E. L., & Loehman, R. E. (2008). Ultra-high-temperature ceramic coatings for oxidation protection of carbon-carbon composites. Journal of the American Ceramic Society, 91(5), 1495-1502.More infoAbstract: Carbon-carbon (C-C) composites are attractive materials for hypersonic flight vehicles but they oxidize in air at temperatures >500°C and need thermal protection systems to survive aerothermal heating. We investigated using multilayers of high-temperature ceramics such as ZrB2 and SiC to protect C-C against oxidation. Our approach combines pretreatment and processing steps to create continuous and adherent high-temperature ceramic coatings from infiltrated preceramic polymers. We tested our protective coatings at temperatures above 2600°C at the National Solar Thermal Testing Facility using controlled cold-wall heat flux profiles reaching a maximum of 680 W/cm2. © 2008 The American Ceramic Society.
- Corral, E. L., Ayala, A. A., & Loehman, R. E. (2008). Evaluation of oxidation protection testing methods on ultra-high temperature ceramic coatings for carbon-carbon oxidation resistance. Ceramic Engineering and Science Proceedings, 28(2), 361-370.More infoAbstract: The development of carbon-carbon (C-C) composites for aerospace applications has prompted the need for ways to improve the poor oxidation resistance of these materials, In order to evaluate and test materials to be used as thermal protection system (TPS) material the need for readily available and reliable testing methods are critical to the success of materials development efforts, With the purpose to evaluate TPS materials, three testing methods were used to assess materials at high temperatures (> 2000°C) and heat flux in excess of 200 Wcm-2. The first two methods are located at the National Solar Thermal Test Facility (NSTTF) at Sandia National Laboratories, which are the Solar Furnace Facility and the Solar Tower Facility, The third method is an oxyacetylene torch set up according to ASTM E285-80 with oxidizing flame control and maximum achievable temperatures in excess of 2000°C In this study, liquid precursors to ultra high temperature ceramics (UHTCs) have been developed into multilayer coatings on C-C composites and evaluated using the oxidation testing methods. The tests will be discussed in detail and correlated with preliminary materials evaluation results with the aim of presenting an understanding of the testing environment on the materials evaluated for oxidation resistance.
- Corral, E. L., Gauntt, B. D., & Loehman, R. E. (2008). Properties of particle-filled glass composites used for sealing solid oxide fuel cells. Ceramic Engineering and Science Proceedings, 28(4), 315-323.More infoAbstract: Sealant materials for solid oxide fuel cells (SOFCs) must meet a demanding set of performance criteria for operating lifetimes of up to 40,000 hr. The resulting seals must be gas tight at temperatures up to 1000°C, resist stresses from thermal gradients and expansion mismatch of different stack materials, and perform reliably over long times at high temperatures in both oxidizing and reducing atmospheres. Ceramic and metal filled glass composite sealants provide for greater design flexibility than other approaches. The seal properties can be tailored by varying the composition, amount, and microstructure of the particulate phase. Composite properties such as glass transition temperature, viscosity, and thermal expansion coefficient can be altered by rational control of the glass chemistry and composite microstructure. Several specific materials combinations have been engineered to meet the demanding set of criteria for sealing materials in SOFCs and characterized by means of viscosity measurements at the proposed operating temperature of 750°C The influence of the matrix/particle interactions has been separated from the mechanical effects of the added phase in studies that systematically vary the chemical composition of the particles. Models for composite suspension viscosity were also used to interpret the observed variation in viscosity with composition and volume fraction of the filler.
- Corral, E. L., III, J. C., Shyam, A., Lara-Curzio, E., Bell, N., Stuecker, J., Perry, N., Prima, M. D., Munir, Z., Garay, J., & Barrera, E. V. (2008). Engineered nanostructures for multifunctional single-walled carbon nanotube reinforced silicon nitride nanocomposites. Journal of the American Ceramic Society, 91(10), 3129-3137.More infoAbstract: Colloidal processing was used to make highly dispersed aqueous composite suspensions containing single-wall carbon nanotubes (SWNTs) and Si 3N4 particles. The SWNTs and Si3N4 particles were stabilized into composite suspensions using a cationic surfactant at low pH values. Bulk nanocomposites containing 1.0, 2.0, and 6.0 vol% SWNTs were successfully fabricated using rapid prototyping. The survival of SWNTs was detected, using Raman spectroscopy, after high-temperature sintering, up to 1800°C. The nanocomposites have densities up to 97% of the composite theoretical density. The engineered nanostructures reveal an increase in grindability and damage tolerance behavior over the monolithic ceramic. We also observed toughening mechanisms such as SWNT crack bridging and pull-out, indicating that SWNTs have the potential to serve as toughening agents in ceramics. Increased fracture toughness values over the monolithic Si 3N4 were observed for the 2.0-vol% SWNT-Si 3N4 nanocomposite when a given sintered microstructure was present. We report here the effects of colloidal processing on mechanical behavior of SWNT reinforced nonoxide ceramic nanocomposites. © 2008 The American Ceramic Society.
- Widgeon, S. J., Corral, E. L., & Loehman, R. E. (2008). Electron microprobe analysis of glass-to-metal seals for use in solid-oxide fuels. Microscopy and Microanalysis, 14(SUPPL. 2), 1424-1425.
- Corral, E. L., III, J. C., Stuecker, J. N., & Barrera, E. V. (2002). Processing of carbon nanofiber reinforced silicon nitride matrix composites. Proceedings of the TMS Fall Meeting, 53-62.More infoAbstract: This work presents a process optimization study for processing vapor grown carbon fibers and single walled carbon nanotubes into Si3N4 with the goal of developing advanced structural ceramic materials. Solid composite specimens were fabricated using a freeform fabrication technique called robocasting that uses high solids loading aqueous suspensions to fabricate near-net-shape-ceramic composite parts. Colloidal processing methods were used to manipulate the charging behavior between carbon nanofibers and silicon nitride particle surfaces in order to develop forty-five percent solids loading suspensions with a pseudoplastic theology that borders on dilatancy and is suitable for robocasting solid parts. Dispersion of nanofibers within each composite system was identified as was the starting dispersion of the nanofibers in the slurry.
- Varma, S. K., Corral, E., Esquivel, E., & Salas, D. (1999). Solutionizing effects on deformation-induced phase transformations in 2014 aluminum composite. Metallurgical and Materials Transactions A: Physical Metallurgy and Materials Science, 30(9), 2539-2545.More infoAbstract: A solutionizing heat treatment of 2014 aluminum alloy reinforced with 0.15 volume fraction of alumina particles (VFAP) results in deformation-induced precipitation during rolling and tensile deformation, with 0.10 VFAP, at room temperature. The extent of precipitation increases with increase in time and/or temperature of solutionizing. An attempt has been made to identify the various types of precipitates in the samples deformed to a given strain and in fractured conditions. The work-hardening curves and tensile properties of the composites have been shown to be dependent on the time and temperature combination of the solutionizing process.
- Varma, S. K., Mahapatra, R., Hernandez, C., Chan, A., & Corral, E. (1999). Influence of processing on microstructures of Ti-44Al-11Nb alloy. Materials and Manufacturing Processes, 14(6), 821-835.More infoAbstract: The cyclic and static oxidation behavior in the processing of Ti-44Al-11Nb alloy has been studied at 900, 950, and 1000 °C in air for a period of up to 168 hours (or a week). A recreation of diffusion paths for the oxide to penetrate into the base metal during every cycle results in the lower oxidation rates during cyclic mode compared to static mode. An extended period of heating time allows for the coarsening of the structure for both forms of alloys: polycrystalline and directionally solidified crystals. Coarsening and phase transformation in the heating period involves large amounts of dislocation activities in the lamellar structure as well as at the interface of lamellar structure and islands of γ.
- Varma, S. K., Salas, D., Corral, E., Esquivel, E., Chawla, K. K., & Mahapatra, R. (1999). Microstructural development during aging of 2014 aluminum alloy composite. Journal of Materials Science, 34(8), 1855-1863.More infoAbstract: The 2014 aluminum alloy reinforced with 0.1 and 0.15 volume fraction of alumina particles (VFAP) have been solutionized for a range of time from 1.5 to 20 h at 813 K. The effect of solutionizing time (ST) on the age hardening response of the composites has been studied and compared with the characteristics exhibited by the monolith. The results indicate that increasing the ST decreases the time required to get the peak hardness (TPH) values in the monolith but the composites do not show a systematic monotonic behavior. The TPH values first decrease and then increase with an increase in ST at an aging temperature of 473 K for the composite. It has been speculated that the ST influences the concentration of quenched-in vacancies and continued heating may affect the bonding between particles and matrix which can generate additional dislocations throughout the solutionizing process due to curvature effects.
- Varma, S. K., Corral, E., Hernandez, C., Mahapatra, R., & Frazier, W. E. (1998). Evolution of microstructures during cyclic and thermal stability of Ti-44Al-11Nb alloy. Proceedings of the TMS Fall Meeting, 15-20.More infoAbstract: A study has been conducted to determine the cyclic and static thermal stability of Ti-44Al-11Nb alloy in air in a range of temperature from 900 to 1000 °C. Weight gain method shows that the static oxidation rates are higher than cyclic oxidation rates under identical experimental conditions at a given temperature. The oxide layer at the surface penetrates the base metal in a direction parallel to the lamellae of the two phases, α2 and γ, confirmed by scanning electron micrographs. The thermal stability of up to 168 hours indicates that there are phase transformations taking placed affecting the microstructures in such a way that large amount of dislocation activities are involved.
- Varma, S. K., Salas, D., Corral, E., Esquivel, E., & Regalado, M. (1998). Microstructures in composites of age hardenable aluminum alloy deformed by room temperature rolling and tensile testing. TMS Annual Meeting, 225-230.More infoAbstract: Age hardenable 2014 aluminum alloys and composites containing 0.10 and 0.15 volume fractions of alumina particles (VFAP) have been solutionized at 540 and 550 °C for up to 20 hours. The solutionized samples, heat treated for 5 and 20 hours, have been subjected to room temperature rolling until cracking develops. The work hardening curves have been compared to determine the effect of solutionizing time on the rolling characteristics from both hardness and the microstructural evolution points of view. Solutionizing at two different temperatures results in differences in the extent to which the composites can be rolled until fracture. The microstructural characterization by TEM has been performed to understand the room temperature rolling behavior.
- Varma, S. K., Salas, D., Ponce, J., Corral, E., Esquivel, E., & Regalado, M. (1997). Influence of solutionizing time and temperature on the bonding characteristics and microstructures between the particles and matrix in composites with 6061 and 2014 aluminum alloys reinforced with alumina particles. TMS Annual Meeting, 287-296.More infoAbstract: The composites of 6061 and 2014 aluminum alloys reinforced with alumina particles have been subjected to solutionizing treatment at 540 °C for various lengths of time up to 20 hours. The two composites show different behavior when the hardness is measured as a function of solutionizing time. The 6061 aluminum alloy containing 0.1, 0.15 and 0.2 volume fractions of alumina (VFAP) show a continuous increase in hardness values as a function of solutionizing time while 2014 alloy shows softening under almost identical experimental conditions. The grain growth law has been found to be observed in both composites and their monoliths. The aging behavior as influenced by the solutionizing seems to be affected by the solutionizing time in an identical fashion. Even though the monoliths indicate a decrease in time required to get the peak hardness (TPH) values the composites show an initial decrease and then increase in TPH values at 200 °C as a function of solutionizing time. The bonding between the particles and the matrix in the two composites has been found to improve as a result of longer solutionizing time as can be seen by the SEM fractographs for the samples deformed to fracture during room temperature tensile testing.
- Varma, S. K., Ponce, J., Andrews, S., Corral, E., & Salas, D. (1996). Microstructures during solutionizing and aging in a 6061 aluminum alloy matrix reinforced with alumina particles. Materials Science Forum, 217-222(PART 2), 931-936.More infoAbstract: The grain growth law has been verified for a range of grain sizes produced in three composites containing 6061 aluminum alloy matrix and 0.10, 0.15 and 0.20 volume fractions of alumina particles (VFAP), with particle sizes of 10, 15 and 20 μm respectively, by solutionizing at 540°C for different times. The solutionizing time affects the (a) microstructures developed at the interface between the particles and the matrices and (b) age hardening characteristics, microstructures and microhardness values, at 200°C.
Proceedings Publications
- Rice, J. A., Hart, M., Corral, E. L., Gou, X., & Kim, D. W. (2017, July). Fabrication and Implementation of a New Ceramic Material in an Adaptive Optics System. In OSA Optical Fabrication and Test.
- Hart, M., Hart, M., Furfaro, R., Furfaro, R., Weiner, B. J., Weiner, B. J., Corral, E. L., Corral, E. L., Lyons, E. H., Lyons, E. H., Surdeanu, M., Surdeanu, M., Butcher, E., Butcher, E., Gaylor, D., Gaylor, D., Jah, M. K., Jah, M. K., Merchant, N. C., , Merchant, N. C., et al. (2016, May). A New Approach to Space Domain Awareness at the University of Arizona. In NATO Symposium on Considerations for Space and Space-Enabled Capabilities in NATO Coalition Operations, SCI-283.
- Hart, M., Hart, M., Jah, M. K., Jah, M. K., Gaylor, D., Gaylor, D., Butcher, E., Butcher, E., Ten Eyck, B., Ten Eyck, B., Corral, E. L., Corral, E. L., Furfaro, R., Furfaro, R., Lyons, E. H., Lyons, E. H., Merchant, N. C., Merchant, N. C., Surdeanu, M., , Surdeanu, M., et al. (2016, May). A New Approach to Space Domain Awareness at the University of Arizona. In NATO Symposium on "Considerations for Space and Space-Enabled Capabilities in NATO Coalition Operations".
Presentations
- Corral, E. L. (2015, Arpil). INVITED: Future of High Temperature Materials. Ceramics EXPO Conference. Cleveland, OH: The American Ceramic Society.
- Corral, E. L. (2015, August). INVITED: Processing of Ultra High Temperature Ceramic Composites Using Spark Plasma Sintering. XXIV International Materials Research Congress, Sociedad Mexicana de Materiales, Symposium on Advanced Structural Materials. Cancun, Mexico: MRS.
- Corral, E. L. (2015, June). INVITED: Oxidation Behavior of Aerospace Materials in High Enthalpy Flows Using and Oxyacetylene Torch Facility. National Space and Missile Materials Symposium (NSMMS) & Commercial & Government Responsive Access to Space Technology (CRASTE), Workshop on Methods of Materials Screening for High Speed Aerospace Applications. Chantilly, VA: NSMMS.
- Corral, E. L. (2015, November). INVITED: Advances in Processing Science and Properties of Carbides, Nitrides, Borides and Graphene Reinforced Ceramic Composites. Mechanical Engineering Department and Materials Science Program Seminar Series. Riverside, CA: The University of California at Riverside.
- Corral, E. L. (2015, October). INVITED: Advances in Processing Science and Properties of Carbides, Nitrides, Borides, and Ceramic Matrix Composites. Air Force Research Laboratory, Materials and Manufacturing Directorate Seiminar. Dayton, OH: Wright Patterson Air Force Research Laboratory.
- Corral, E. L. (2015, October). INVITED: Oxidation Behavior of Aerospace Materials in High Enthalpy Flows Using and Oxyacetylene Torch Facility. Materials Science & Technology 2015 Conference, Symposium on Thermal Protection Materials and Systems and Session on Challenges of Aggressive Environments: Oxidation, Degradation and Heat Rejection. Columbus, OH: The American Ceramic Society, American Society for Materials.
- Corral, E. L. (2015, October). INVITED: Precision Processing of Ultra-high Purity Ceramics using Spark Plasma Sintering and Thermodynamics. 2015 CNMS User Meeting: Planning Center for Nanoscale Materials Science (CNMS) Science for its 2nd Decade, Session on Buried Interface Structure and Effects on Properties. Oak Ridge, TN: ORNL.
- Corral, E. L. (2015, October). Oxidation of Aerospace Materials in High Enthalpy Flows Using and Oxyacetylene Torch Facility,. 7th Ablation Workshop. Tullahoma, TN: NASA/AFOSR/SNL/UTSI.
- Corral, E. L. (2016, September). INVITED: Precision Processing of Ultra-high Purity Ceramics using Spark Plasma Sintering and Thermodynamics. Materials Directorate at Army Research Laboratory. Adelphi, MD: Army Research Laboratory.
- Corral, E. L. (2014, April 28). INVITED: Direct Current Sintering of Metallic Ceramics. Department of Chemical Engineering and Materials Science Seminar. Davis, California: University of California at Davis.
- Corral, E. L. (2014, January 27). Self Protective Coatings on C-C Composites for High Temperature Oxidation Resistance Using UHTCs. 38th International Conference and Exposition on Advanced Ceramics and Composites, Symposium on Materials for Extreme Environments: Ultra-high Temperature Ceramics (UHTCs) and Nanolaminated Ternary Carbides and Nitrides (MAX Phases. Daytona Beach, FL: ACerS-Engineering Ceramics Division.
- Corral, E. L. (2014, January 29). INVITED: Rapid Joining of UHTCs, Carbides, and Nitrides Using Spark Plasma Joining. 38th International Conference and Exposition on Advanced Ceramics and Composites, Symposium on Materials for Extreme Environments: Ultra-high Temperature Ceramics (UHTCs) and Nanolaminated Ternary Carbides and Nitrides (MAX Phases), Session on Novel Joining and Machining of Components. Daytona Beach, FL: The American Ceramic Society-Engineering Ceramics Division.
- Corral, E. L. (2014, July 29). INVITED: High Temperature Ceramics, Coatings and Joining of Ceramics. Future of High Temperature Materials Workshop. Boulder, CO: The University of Colorado-Boulder.
- Corral, E. L. (2014, June 11). INVITED: Advances in Ultra-High Temperature Ceramic Research at UofA. CIMTEC 2014: Symposium CF1-High Temperature Ceramics for Extreme Environments. Montecatinni Terme, Italy: International Conferences on Modern Materials and Technologies.
- Corral, E. L. (2014, June 17-19). KEYNOTE: High Temperature Isothermal Oxidation Behavior of Ceramic Matrix Composites for Application in Extreme Aerospace Environments. HITEMP 2014 Conference. Santa Fe, NM.
- Corral, E. L. (2014, June 27). KEY NOTE PRESENTATION: The Future of High Temperature Materials. Raytheon Missile Systems Engineering Technology Day. Raytheon Missile Systems Campus, Tucson, AZ: Materials and Nanotechnology Division.
- Corral, E. L. (2014, June 6). INVITED: Direct Current Sintering of Metallic Ceramics. Institute for Science and Technology of Ceramics (ISTEC) Seminar. Faenza, Italy: ISTEC.
- Corral, E. L. (2014, November 6). High Temperature Aerospace Materials. Air Force Research Laboratory Director Site Visit. The University of Arizona.
- Corral, E. L. (2014, October 14). INVITED: Carbon Oxidation Testing and Characterization of High Enthalpy Flows for CFD Models. Materials Science and Technology 2014 Conference and Exhibition, Symposium on Thermal Protection Materials and Systems. Pittsburgh, PA: ACerS, TMS, ASM International.
- Corral, E. L. (2014, October 30). INVITED: Oxidation of Aerospace Materials Using High Enthalpy Flows. Aerospace and Mechanical Engineering Department Seminar. Tucson, AZ: The University of Arizona.
- Ellis, A., Pinc, W., & Corral, E. L. (2014, January 30). Microstructural control of spark plasma sintered silicon nitride powder blends. 38th International Conference and Exposition on Advanced Ceramics and Composites, Symposium on Mechanical Behavior and Performance of Ceramics and Composites. Daytona Beach, FL: The American Ceramic Society.
- Miller, M., & Corral, E. L. (2014, January 29). Dynamic NonEquilibrium Oxidation of UHTCs. 38th International Conference and Exposition on Advanced Ceramics and Composites, Symposium on Materials for Extreme Environments: Ultra-high Temperature Ceramics (UHTCs) and Nanolaminated Ternary Carbides and Nitrides (MAX Phases). Daytona Beach, FL: The American Ceramic Society.
- Miller, M., Neff, P. K., Packard, M., Walker, L. S., & Corral, E. L. (2014, January 28). Comparing Oxyacetylene Torch Testing and Furnace Facilities for Oxidation of Aerospace Materials. 38th International Conference and Exposition on Advanced Ceramics and Composites, Symposium on Materials for Extreme Environments: Ultra-high Temperature Ceramics (UHTCs) and Nanolaminated Ternary Carbides and Nitrides (MAX Phases). Daytona Beach, FL: American Ceramic Society-Engineering Ceramics Divison.
- Pham, D., & Corral, E. L. (2014, January 28). Densification and Scale up and Mechanical Properties of Direct Current Sintered High Purity ZrB2. 38th International Conference and Exposition on Advanced Ceramics and Composites, Symposium on Materials for Extreme Environments: Ultra-high Temperature Ceramics (UHTCs) and Nanolaminated Ternary Carbides and Nitrides (MAX Phases). Daytona Beach, FL: The American Ceramic Society.
- Pham, D., & Corral, E. L. (2014, January 29). Direct Current Sintering for Rapid, Large Scale Densification of Zirconium Diboride Ceramics. 38th International Conference and Exposition on Advanced Ceramics and Composites, Symposium on International Symposium on Advanced Processing and Manufacturing Technologies for Structural and Multifunctional Materials and Systems (APMT8) in Honor of Prof. Stuart Hampshire. Daytona Beach, FL: The American Ceramic Society.
- Pham, D., Pinc, W., & Corral, E. L. (2014, January 29). Direct Current Sintering for Rapid, Large Scale Densification of Silicon Nitride Ceramics. 38th International Conference and Exposition on Advanced Ceramics and Composites, Symposium on International Symposium on Advanced Processing and Manufacturing Technologies for Structural and Multifunctional Materials and Systems (APMT8) in Honor of Prof. Stuart Hampshire. Daytona Beach, FL: The American Ceramic Society.
- Schnittker, K., & Corral, E. L. (2014, January 30). Bulk Mechanical Properties of Graphene-Silicon Nitride Ceramics. 38th International Conference and Exposition on Advanced Ceramics and Composites, 8th International Symposium on Nanstructured Materials and Nanocomposites. Daytona Beach, FL: The American Ceramic Society.