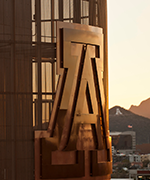
Hannah D Budinoff
- Assistant Professor, Systems and Industrial Engineering
- Member of the Graduate Faculty
- (520) 621-3032
- ENGINEERING, Rm. 221
- TUCSON, AZ 85721-0020
- hdb@arizona.edu
Biography
Dr. Hannah Budinoff is an Assistant Professor of Systems and Industrial Engineering at the University of Arizona. Her research interests include additive manufacturing, geometric manufacturability analysis, design for manufacturing, sustainable design, and engineering education. She completed her PhD in 2019 in mechanical engineering at the University of California, Berkeley, where she was awarded an NSF Graduate Research Fellowship. She oversees the Manufacturing and Design Exploration (MADE) research group at the University of Arizona (https://sites.arizona.edu/made-lab/).
Degrees
- Ph.D. Mechanical Engineering
- University of California, Berkeley, Berkeley, California, United States
- M.S. Mechanical Engineering
- University of California, Berkeley, Berkeley, California, United States
- B.S. Mechanical Engineering
- University of Arizona, Tucson, Arizona, United States
Awards
- Remote Learning ABCs Competition
- New Engineering Educators Division of the American Society for Engineering Education, Summer 2021 (Award Finalist)
- Apprentice Faculty Grant
- Educational Research and Methods Division of the American Society for Engineering Education, Spring 2021
- Best Paper Award
- ASEE Design Graphics Division, Summer 2019
- Best diversity paper nominee
- ASEE Annual Conference and Exposition, Summer 2019
- Design Essay Competition winner
- NSF/American Society of Mechanical Engineers, awarded at ASME IDETC/CIE, Summer 2019
- Graduate Research Fellowship
- National Science Foundation, Fall 2015
Interests
Teaching
Engineering design; Additive manufacturing
Research
Design for additive manufacturing; Manufacturability analysis; Engineering education; Sustainable design; Sustainable manufacturing
Courses
2025-26 Courses
-
Dissertation
SIE 920 (Fall 2025) -
Intro Engr Design
ENGR 102B (Fall 2025) -
Research
SIE 900 (Fall 2025)
2024-25 Courses
-
Dissertation
SIE 920 (Spring 2025) -
Int Manufacturing Sys
SIE 383 (Spring 2025) -
Master's Report
SIE 909 (Spring 2025) -
Research
SIE 900 (Spring 2025) -
Design for Addit Manuf
SIE 481 (Fall 2024) -
Design for Addit Manuf
SIE 581 (Fall 2024) -
Dissertation
SIE 920 (Fall 2024) -
Master's Report
SIE 909 (Fall 2024)
2023-24 Courses
-
Dissertation
SIE 920 (Spring 2024) -
Int Manufacturing Sys
SIE 383 (Spring 2024) -
Research
SIE 900 (Spring 2024) -
Directed Research
SIE 492 (Fall 2023) -
Dissertation
SIE 920 (Fall 2023) -
Research
SIE 900 (Fall 2023)
2022-23 Courses
-
Master's Report
SIE 909 (Summer I 2023) -
Directed Research
SIE 492 (Spring 2023) -
Dissertation
SIE 920 (Spring 2023) -
Int Manufacturing Sys
SIE 383 (Spring 2023) -
Master's Report
SIE 909 (Spring 2023) -
Research
SIE 900 (Spring 2023) -
Design for Addit Manuf
SIE 481 (Fall 2022) -
Design for Addit Manuf
SIE 581 (Fall 2022) -
Dissertation
SIE 920 (Fall 2022) -
Intro Engr Design
ENGR 102B (Fall 2022)
2021-22 Courses
-
Internship
SIE 593 (Summer I 2022) -
Intro Engr Design
ENGR 102B (Fall 2021) -
Research
SIE 900 (Fall 2021) -
Senior Dsgn Projects II
SIE 498B (Fall 2021)
2020-21 Courses
-
Senior Design Projects I
SIE 498A (Spring 2021) -
Special Topics in SIE
SIE 496 (Fall 2020) -
Special Topics in SIE
SIE 596 (Fall 2020)
2019-20 Courses
-
Intro Engr Design
ENGR 102B (Spring 2020)
Scholarly Contributions
Journals/Publications
- Budinoff, H. D., & Kramer, J. (2022). ‘Earning your scars’: an exploratory interview study of design for manufacturing at hardware startups. Research in Engineering Design. doi:10.1007/s00163-022-00396-x
- Budinoff, H. D., & Shafae, M. (2022). Connecting part geometry and cost for metal powder bed fusion. International Journal of Advanced Manufacturing Technology. doi:10.1007/s00170-022-09688-x
- Budinoff, H. D., & McMains, S. (2021). Will it print: a manufacturability toolbox for 3D printing. International Journal on Interactive Design and Manufacturing, 15(4), 613-630. doi:https://doi.org/10.1007/s12008-021-00786-w
- Budinoff, H. D., Bushra, J., & Shafae, M. (2021). Community-Driven PPE Production using Additive Manufacturing During the COVID-19 Pandemic: Survey and Lessons Learned. SME Journal of Manufacturing Systems.
- Budinoff, H. D., Bushra, J., & Shafae, M. (2021). Community-driven PPE production using additive manufacturing during the COVID-19 pandemic: Survey and lessons learned. Journal of Manufacturing Systems. doi:10.1016/j.jmsy.2021.07.010More infoThis study presents a detailed analysis of the production efforts for personal protective equipment in makerspaces and informal production spaces (i.e., community-driven efforts) in response to the COVID-19 pandemic in the United States. The focus of this study is on additive manufacturing (also known as 3D printing), which was the dominant manufacturing method employed in these production efforts. Production details from a variety of informal production efforts were systematically analyzed to quantify the scale and efficiency of different efforts. Data for this analysis was primarily drawn from detailed survey data from 74 individuals who participated in these different production efforts, as well as from a systematic review of 145 publicly available news stories. This rich dataset enables a comprehensive summary of the community-driven production efforts, with detailed and quantitative comparisons of different efforts. In this study, factors that influenced production efficiency and success were investigated, including choice of PPE designs, production logistics, and additive manufacturing processes employed by makerspaces and universities. From this investigation, several themes emerged including challenges associated with matching production rates to demand, production methods with vastly different production rates, inefficient production due to slow build times and high scrap rates, and difficulty obtaining necessary feedstocks. Despite these challenges, nearly every maker involved in these production efforts categorized their response as successful. Lessons learned and themes derived from this systematic study of these results are compiled and presented to help inform better practices for future community-driven use of additive manufacturing, especially in response to emergencies.
- Budinoff, H. D., & Mcmains, S. (2020). Improving Outcomes and Participation in the Prototyping Process Using Design-for-Additive-Manufacturing Training. International Journal of Engineering Education, 36(4), 1170-1183.
- Budinoff, H. D., McMains, S., & Rinaldi, A. (2018). An interactive manufacturability analysis and tolerance allocation tool for additive manufacturing. Proceedings of the 2018 ASME IDETC-CIE Conference, 2A.
- Budinoff, H., & McMains, S. (2018). Prediction and visualization of achievable orientation tolerances for additive manufacturing. Procedia CIRP, 75, 81-86.
- Budinoff, H., & McMains, S. (2018). Relationships between spatial visualization ability and student outcomes in a 3D modeling course. The Engineering Design Graphics Journal, 82(2).
- Budinoff, H., Bhinge, R., & Dornfeld, D. (2016). A material-general energy prediction model for milling machine tools. Proceedings of the 2016 International Symposium on Flexible Automation (ISFA), 161-164.
Proceedings Publications
- Budinoff, H., Berger, E., Bushra, J., & Shivers-McNair, A. (2023). Board 424: Using Badging to Promote Makerspace Participation and Engineering Identity Development: Emergent Themes and Lessons Learned from a Pilot. In ASEE.
- Budinoff, H., Wessman, A., & Chauhan, K. (2023). Using online learning modules to improve students’ use of technical standards in additive manufacturing courses and projects. In ASEE.
- Bushra, J., Budinoff, H. D., Luna Falcon, P., & Latypov, M. (2023). Enhancing Design Guidelines for Metal Powder Bed Fusion: Analyzing Geometric Features to Improve Part Quality. In IDETC/CIE.
- Manford, D., Budinoff, H. D., Callaghan, B. J., & Jeon, Y. (2023). Towards a general model to predict energy consumption for fused filament fabrication. In NAMRC/MSEC.
- Budinoff, H., Subbian, V., & Lopez, F. (2022). Integrating Asset-based Practices into Engineering Design Instruction. In ASEE.
- Manford, D., Budinoff, H. D., & Bushra, J. (2022). Accuracy of build time and mass estimates from slicer software for fused filament fabrication. In NAMRC/MSEC.More infoThere is growing interest to optimize the fused filament fabrication process to produce quality products and make it more energy efficient. One of the ways to help achieve this is by initially obtaining accurate build time and mass estimates from 3D printing slicer software to assess the energy consumed by 3D printers. This paper aims to compare the accuracy of build time and mass estimates of three different slicer programs, including Simplify3D, Cura and PrusaSlicer, through experiments for certain parameter settings. An Ultimaker 3 and Prusa i3 MK 3S+ printer are used for the estimates and actual experiments. The mean absolute error for each slicer software is quantified and the results are compared to assess accuracy. The mean absolute error of the build time estimate for Simplify3D, Cura, and PrusaSlicer was 55.25 min, 49.5 min, and 203.25 min, respectively. The mean absolute error of the mass estimate for Simplify3D, Cura, and PrusaSlicer was 4.49 g, 6.25 g, and 9.07 g respectively. The results show that slicer software tend to overestimate mass, while over or under predicting build time, depending on the printer and process parameters. Simplify3D and Cura provide the most accurate build time and mass estimates. The results indicate that Simplify3D and Cura estimates show promise for use in energy efficiency and material consumption analysis.
- Budinoff, H. D. (2021). Asset-based Approaches to Engineering Design Education: A Scoping Review of Theory and Practice. In ASEE Annual Conference and Exposition.
- Budinoff, H. D., Sun, Y., & McMains, S. (2021). Comparison of Real-Time Geometric Analyses to Predict Warping Deformation in Fused Filament Fabrication. In NAMRC/MSEC.
- Budinoff, H., & Subbian, V. (2021). Asset-based Approaches to Engineering Design Education: A Scoping Review of Theory and Practice. In ASEE.
- Bushra, J., & Budinoff, H. D. (2021). Orientation Optimization in Additive Manufacturing: Evaluation of Recent Trends. In ASME International Design Engineering Technical Conferences and Computers and Information in Engineering Conference.
- Bushra, J., & Budinoff, H. D. (2021). Orientation Optimization in Additive Manufacturing: Evaluation of Recent Trends. In IDETC/CIE.
- Budinoff, H. D. (2020, June). Engineering Graphics in a Community College Setting: Challenges and Opportunities. In ASEE Annual Conference & Exposition.
- Budinoff, H. D., Sun, Y., & McMains, S. (2020, August 2020). Comparison of Real-Time Geometric Analyses to Predict Warping Deformation in Fused Filament Fabrication. In ASME International Manufacturing Science and Engineering Conference, 84256.
- Budinoff, H. D. (2019). Underrepresented and International Student Success and Confidence in a Small, Lab-based CAD Class. In ASEE EDGD 73rd Mid Year Conference.
- Budinoff, H. D., McMains, S., & Ford, A. C. (2020). Effects of Gender, Effort, and Spatial Visualization Abilities in an Engineering Graphics Class. In ASEE.
- Budinoff, H. D. (2018). Measuring and Predicting Achievable Tolerances for AM Processes. In ISAM.
- Budinoff, H. D., & McMains, S. (2018). Relationships between Spatial Visualization Ability and Student Outcomes in a 3D Modeling Course.. In ASEE.More infoThe impact of spatial visualization ability on student outcomes in a freshman-level, 3D modeling class is explored by analyzing connections between students’ spatial ability pre- and post-test scores, course grades, and self-reported difficulty of an assignment. Analysis of the results indicate that spatial visualization ability, as measured by the post-test, is strongly correlated with perceived difficulty, exam grades, and overall course grade. Students’ spatial visualization scores increased over the semester by an average of 9.4%; however, students with low spatial visualization ability underperform compared to their peers.
- Budinoff, H. D., Rinaldi, A., & McMains, S. (2018). An Interactive Manufacturability Analysis and Tolerance Allocation Tool for Additive Manufacturing. In ASME IDETC/CIE.More infoGeometric tolerances for new products are sometimes assigned without specific knowledge of the cost or feasibility of manufacturing them to the assigned tolerances, which can significantly drive up production costs and lead to delays and design revisions. We present an interactive tool that quickly estimates the manufacturability of assigned tolerances for additive manufacturing and a compact visualization to present this information to the designer. The designer can use the system to explore feasible build orientations and then adjust specified tolerance limits if all tolerances are not simultaneously achievable at a single orientation. After the designer is satisfied that the range of feasible orientations has been fully explored, a physical programming approach is used to identify a single orientation to best satisfy the designer’s preferences. The calculation and visualization of the results is done in real-time, enabling quick iteration. A test case is presented to illustrate the use of the tool.